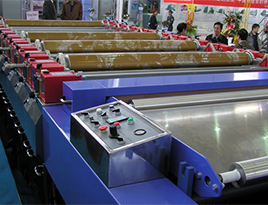
1. The introduction
Rotary screen printing machine is the main equipment for printing production in textile printing and dyeing industry. According to the transmission mode of rotary screen, it can be divided into mechanical integral transmission rotary screen printing machine and independent transmission rotary screen printing machine. The rotary screen printing machine is usually composed of feeding unit, printing unit, drying unit and blanking unit, among which the printing unit is the core part of the whole equipment
2. Equipment composition of rotary screen printing machine
Rotary screen printing machine is a special production equipment that uses round nickel net to continuously print all kinds of patterns on white grey cloth. Its working principle is similar to that of color printing machine. The whole machine includes four parts: feed cloth, main machine, drying room and drop cloth. Host part is composed of main motor after worm gear and worm reducer drive a diameter of about 450 mm (long ranged from 1.8 meters to 3 meters) roller, roller to drive more than two millimeters thick polyurethane conduction band, by the passive roller diameter smaller taut conduction band, make no slippage between the roller and the conduction band and conduction band form a plane between two rollers, the fabric was against conduction band by monochromatic mesh at the end of the day the bit into the dryer to dry the cloth. As long as the mesh is strictly synchronized with the guide belt, and there is no error in the phase at any time between the mesh, the printing accuracy of 0.1 mm can be strictly maintained in the high-speed movement (the extreme speed limit is 120 m/min) (which is also the precision of the printing guide belt). Just like the application of numerical control technology in machine tools, the advanced rotary screen printing machine uses the net head single motor drive technology to eliminate the backward way of mechanical reducer long shaft drive, and overcomes the influence of the original mechanical drive clearance and wear on printing. Compared with the numerical control machining technology, it is a high-speed and high-precision synchronization technology, and there can be no obvious speed and position error in the speed of lifting. And can not be as CNC sometimes need to reduce the feed speed to ensure a small error. Full servo rotary screen printing machine refers to the main motor and the independent transmission motor of the network head are driven by WinMO servo SD-100 motor, and the input and outlet motor are driven by WinMO frequency converter model VFT0022T4. Operation is controlled by Winmo touch screen.
The outline of the rotary screen printing machine is shown in Figure 1
Fig. 1 Outline drawing of rotary screen printing machine
3. Brief introduction to the principle of rotary screen printing machine
The electronic control system of the rotary screen printing machine is composed of two parts. Based on the advanced electronic technology developed at the bottom, the high-speed and high-precision synchronous motion control is realized, so that the servo motor of the net head can accurately track the distribution speed (which is indirectly obtained by measuring the angular speed of the main roller by the high-resolution encoder). Achieve color printing. The changing location information can be processed online by the system in as little as 10 microseconds. Therefore, the speed can be reduced from 80 meters per minute to zero in one second without much position error, which can be compared with advanced foreign systems. The other part is realized by the numerical control of the machine from the cloth into the cloth to the cloth out of synchronous drag control and operation control, with a touch screen to complete the speed simulation bar display, speed up and down of different speed segments of the shortcut key one-key operation, and fault scrolling display.
For dyeing and printing of grey fabric by unit is passed to the guide bring into cloth, due to the conduction band surface coated with a layer of special glue, beforehand for grey cloth can close contact with the conduction band, won't produce relative motion, and the conduction band close contact of fabric with the movement of the conduction band, through various printing single round, by silk screen printing unit (carving patterns, dye through the screen inside circle as WangTou the rotation of the seepage on the fabric, thus forming a kind of color design, the silk screen design on the different printing unit form different color pattern, in order to ensure that the various color patterns and eventually build up a complete graph, Phase must ensure a constant between each screen, that is, to achieve high quality, automated printing production, between the cylinder and the conduction band and rotary screen, in a row, running at a high speed must implement high precision synchronous control, the printing conduction band cylinder linear velocity and linear velocity must ensure that synchronization, otherwise it will produce cloth, broken broken network or "wrong" accident, affects the production efficiency and product quality
The servo driver receives the impulse instruction to drive the motor to drive the machine to make the positioning movement. In the process of positioning operation, the operation should be smooth and smooth. The running speed of the servo will determine whether the working efficiency of the rotary screen printing machine can meet the application requirements of customers. In the case of high-speed positioning, the servo motor should not appear overshoot, shock or too long setting time
4. Winmo servo system configuration
The difficulty in debugging is how to ensure a good printing effect, which requires the printing net head and the printing guide belt to keep a high degree of synchronization. Only if the phase Angle between the circular net and the guide band is kept constant, can the pattern be ensured to be in good position. Winmo servo can guarantee the synchronization of speed and position at the same time. The phase of each roller should be consistent at all times. By dynamically adjusting the electronic gear ratio parameters in the drive, the gear clearance can be eliminated during gear transmission, which greatly facilitates the debugging of the system and ensures the precision of printing cloth. Set servo control mode, gear ratio and other parameters, and then carry out reciprocating motion test, if the positioning and speed accuracy meet the requirements, the debugging is completed; If you do not meet the requirements, then increase the speed loop gain, at this time if the motor stops overshoot or jitter, a noise or motor, so that the loop control parameter tuning some too, again appropriate proportion decrease or increase the integral time constant, until the precision of position and velocity are up to par, shows the proportion of the position loop and speed loop and integral time constant value for the appropriate value.
Nantong a round screen printing machine, the use of WinMO series full digital SD-100 servo drive. The main parameter setting of the control system is described as follows:
PA4=0 (control mode selection, 0: position control);
PA1=1 (motor type selection, the parameters are different for different motors);
PA9=500 (position loop gain, range 1 -- 1000ms);
PA5=500 (speed loop gain, range 5 -- 2000Hz);
PA6=100 (Velocity loop integral time constant, range 1 -- 1000ms);
PA14=0(input form of instruction pulse, range 0 -- 2);
PA12=10(input instruction pulse frequency doubling molecule);
PA13=1(denominator of input instruction pulse frequency doubling);
PA60=1000 (current loop gain, range 500 -- 8000);
PA61=10 (current loop integral time constant, range 10 -- 50);
Note: Electronic Gear Ratio =PA12/PA13== PPULSE /P
Wherein, PPULSE refers to the number of pulses fed back by the motor feedback element for one turn of motor rotation (pulses/turns). For example, for an incremental encoder with 2500 lines, the number of pulses fed back to the driver is 2500×4=10000;
P: Indicates the number of instruction pulses (pulses/turns) received by the upper computer to make the motor rotate for one turn of the servo;
5. Debugging matters needing attention
In order to ensure the reliable, stable and correct operation of the servo driver, the following matters should be paid attention to during the installation, debugging and use of the servo system:
1. Correct wiring: WinMO servo encoder line and motor power line are standard. When wiring, the signal line between the servo driver and the controller must be connected correctly, otherwise the servo will not operate normally.
2. Correct setting of the servo control mode: As each machine application is different, the correct setting of the servo control mode is the premise to ensure the correct operation of the servo.
3. Match the gain parameters correctly according to the actual operation effect.
4. Ensure that the motor is well grounded and the driver is connected to the equipment housing. On the one hand to avoid interference, on the other hand to avoid leakage.
5. Signal lines should be shielded twisted pair as far as possible, and the shielding layer is generally connected to the terminal shell.
6. Pay attention to interference to avoid interference of encoder signals and control signals. Encoder and signal lines should not be tied together with motor lines and power lines or pass through a cable slot, and try to keep a certain distance.
7. Conclusion
The rotary screen printing machine fully combines the advantages of WinMO servo, such as fast response, accurate positioning, short setting time and smooth operation, so that customers can achieve good satisfaction. The system has been put into operation since September 2013, and the system is in good running condition. This equipment fully demonstrates the advantages of WINMO servo to customers, and also improves the competitiveness of rotary screen printing machine equipment in the market.